A unique solution which combines video and digital printing: no one has heard of anything similar up to now.
When Iggesund Paperboard planned the first digitally printed cover for its inspirational magazine Inspire, the ambition level was high. The whole issue was devoted to the possibilities of digital print, and one of the goals was to produce 22,000 unique covers in a way never done before.
Iggesund Paperboard is part of the Swedish forest industry group Holmen, one of the world’s 100 most sustainable companies listed on the United Nations Global Compact Index. Iggesund’s turnover is just over €500 million and its flagship product Invercote is sold in more than 100 countries.
The company has two brand families, Invercote and Incada, both positioned at the high end of their respective segments.
Since 2010 Iggesund has invested more than €380 million to increase its energy efficiency and reduce the fossil emissions from its production.
Unique solution
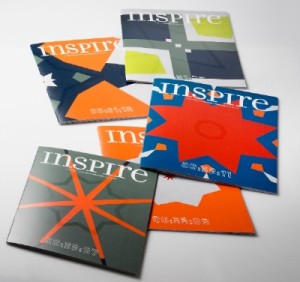
Each and every one of the 22,000 covers of Iggesund Paperboard’s inspirational magazine Inspire is unique, with variable printing of colour fields, varnish patterns and time codes.
Just adding a recipient’s name or a serial number was a bit too easy. More interesting was to start from Inspire’s tradition of using graphics on its cover.
The Inspire editorial team created a 16-minute-long film where each frame was then used as a cover.
«It might seem like a roundabout procedure but it was far simpler than creating 22,000 individual print files using layout software» Thomas Idebäck, Motion Graphic Designer, says.
The variation in the printed covers lies partly in the colour fields but also in the spot varnish. The colour field variations by themselves make each cover unique but the varnish patterns also vary.
Each cover is also marked with the time code of the particular film frame on which it is based.
Digaloo digital printers in Stockholm were sent the 1.4 TB of raw data that had to be processed into pages. As the work progressed, the amount of data being processed grew to between 3.5 and 4 TB. Fortunately the printers had invested in a new press and a RIP (Raster Image Processor) IN-100 to increase their processing capacity.
«This print run is totally unique. I’ve talked with colleagues in my international network of digital printers and no one has heard of anything similar» says Jannes Dahlgren, CEO of Digaloo.
The company took 27 hours of active printing time to complete the project.
Scrivi un commento